What is Digital Twins Technology? (Definition, Examples, and Benefits)
Authors: Alex Dzyuba, Lucid Reality Labs Founder & CEO
Table of Contents
Today, the concept of Digital Twins has become a great point of interest, with more people trying to understand what is Digital Twins technology and what lies behind them, whether it is correct to refer to it as “3D Digital Twins”. It is no surprise, as the global Digital Twin implementation is rapidly accelerating, driven by the Manufacturing and Healthcare sectors. The technology market is growing at 60,6% CARG, projected to reach USD 73.5 billion by 2027. At the same time, Gartner predicts Digital Twins as one of the technologies, along with Web3 and spatial computing, to be leveraged by 40% of global organizations to accelerate revenue in their Metaverse-based projects. Nevertheless, many are yet to grasp the concept behind it and are seeking to understand how Digital Twins can be leveraged in the rapidly accelerating, technologically infused market to enhance their industry or sector. To bring in some clarity, we decided to dedicate this article to going over the definition, industry examples, a couple of real use cases, and the long-term benefits organizations and businesses can take advantage of.
Digital Twins Definition
A Digital Twin is a virtual counterpart, a 1-to-1 representation of a physical object, asset, environment, process, or entire ecosystem. Digital Twins are developed using real-time data, 3D modeling and animation, logic, and architecture replication, such as visual and physical characteristics, environmental conditions, operational data, and responses. The technology approach simulates the behavior and performance of the physical object, environment, or complete systems recreated in a digital space. Digital Twins can be used to enhance a variety of industries, including Healthcare, MedTech, Pharma, Aerospace, Defense, Engineering, Manufacturing, and many more.
The technology can be incorporated into processes regardless of scale and complexity, including engineering design, performance optimization, predictive maintenance, remote monitoring and servicing, as well as scenario reconstruction. They enable testing, analysis, monitoring, and reiterating the performance of real-time physical systems or objects under different conditions and scenarios, including but not limited to making informed, data-driven decisions.
Digital Twins Examples
The Digital Twins approach enables the development of full-scale, fully functional, high-fidelity digital representations; thus, the technology finds vast implementation across industries. Automotive & Transportation implementation predicting the most rapid growth by 2023 amongst Aerospace & Defense, Healthcare, Home & Commercial, Energy & Utilities, and Oil & Gas industries.
Digital Twins are being used for various activities, including but not limited to simulation and testing of physical systems and processes, providing specialists with real-time insights, modeling, reenacting scenarios, or even recreating conditions to train informed decision-making. They can be classified into System Digital Twins, Product Digital Twins, and Process Digital Twins. That said, we would like to highlight several industries accelerating the Digital Twins technology implementation today and illustrate some real cases developed for Healthcare, MedTech, and Aerospace.
Digital Twins in Healthcare
Digital Twins open a vast scope of new possibilities for Healthcare. The global market was estimated at US$ 448.9 million in 2021 and is expected to surpass US$ 5.3 billion by 2031. The technology can be used to enhance training and education, diagnostics, planning, hands-on practice, walk-throughs, and much more. They enable medical specialists to submerge and operate in any environment, including fully recreated medical facilities, facing real-life scenarios without posing a threat to a real patient’s life. The concept of Health Digital Twin (HDT) is becoming one of the drivers in medical innovation, becoming more vastly incorporated into public health, precision medicine, and clinical trial. The Health Digital Twin approach can incorporate specific patients’ medical history, biological data, real-time sensors, and multimodal patient data, or population data, enhanced with variables of patient and environment data updates. Combined with AI, the technology can be leveraged to monitor, diagnose, optimize treatment, and predict disease.
Digital Twins in Medical Devices
The global medical devices market is estimated to reach $718.92 billion by 2029, driven by an increase in chronic disease numbers, early diagnostics, and treatment, resulting in inpatient admissions and diagnostic and surgical procedures. Digital Twins can be especially helpful as the approach enables to recreate and simulate any regulatory class medical devices. The technology allows the building of complete digital replicas that medical device manufacturers and medical institutions around the globe can use. With Digital Twins, it is possible to experience and practice using a medical device of any scale regardless of the users’ physical location. It can be used to showcase and test medical devices prior to medical institution distribution and patient implementation, educating and hands-on training medical specialists on new or existing devices, innovative procedures, and approaches in a recreated, fully functional, interactive medical environment.
Digital Twins in Aerospace
Digital Twins has already received a wide application in the Aerospace industry. The approach can be used to design, visualize and recreate fully functional replicas of complete military and commercial carriers, missiles, space, and aviation projects. Digital Twins can be leveraged for Aerospace industry environments and components like cockpits, cabins, engines, or even weather conditions, enhanced by real-time data from sensors to predict performance and wear, fault diagnosis, enhance training, predictive analysis, enable proactive maintenance, improve efficiency and safety. Digital Twins’ incorporation into Aerospace allows reenacting research, design, production, and maintenance processes, reducing unplanned systems or aircraft downtime. Even though NASA and its Apollo project are referred to as one of the major implementations of Digital Twins in the Aerospace industry, some sources indicate that this example could be stretching it a bit far from the concept of this technology. At the same time, companies like Boeing are investing in incorporating Digital Twin technology into their maintenance and manufacturing processes. While, three quarters of the global Air Force executives express their confidence in the Digital Twin implementation.
Digital Twins in Manufacturing
A Digital Twin implementation in the Manufacturing industry is reportedly connected to the cost reduction market demand, the rise of Industry 4.0, and the smart manufacturing approach. Leveraging Digital Twins can be integrated into practically any stage of the manufacturing process, starting from design and modeling to production and maintenance. The technology can be used to recreate a digital counterpart of the entire manufacturing process, allowing engineers to optimize production, reduce downtime, and improve efficiency. It allows leveraging pattern recognition and big data processing, enabling physical to digital operations and activities synchronization, thus resulting in supply chain improvement, minimizing failure rates, and reducing both the development cycle and costs. In their 10-year technology outlook on the 2030 simulation and Digital Twin, Siemens predicts a smoother and broader incorporation of highly dynamic, fully immersive digital counterparts within and outside Manufacturing.
Digital Twins in Oil and Gas
Global Oil and Gas production is one of the most significant fractions of the worldwide economy. Global industry revenue reached $4 trillion in 2022, with the entire sector comprising exploration, production, maintenance, transportation, refinement, and other companies. The industry is driven by several factors, including the need for performance and productivity improvement accelerated by technological adaptation and Big Data. The Digital Twins are defined among the disruptive innovation tools, as their implementation can be used to advance both processes and performances, including planning, risk mitigation, predictive assessment and maintenance, drilling and fossil fuel extraction optimization, extraction site, facilities and plants management, and much more. The technology can help reduce costs, and plan and monitor the process, providing specialists with data necessary for effective decision-making. Today, over 40 Oil and Gas companies are reportedly seeking to take advantage of the Digital Twin Technology potential implementation.
Digital Twins in Construction
With the Construction industry being amongst the largest in the world economy, reaching nearly 12.74 trillion in 2022, the Digital Twins technology has quite the expectations in the industry, with fairly challenging promises, including a significant digital transformation, change of status quo, and improvement of value, productivity, and efficiency. It is unsurprising, as the Digital Twins technology can deliver significant value in transparency, real-time monitoring, feedback, and analysis. The technology can be leveraged to create virtual models of buildings, enabling the design and testing of various configurations, monitor progress, identify potential issues, improve project management, optimize technical scheduling, reenact resource use and optimization scenarios, or even run scenarios to test improvements of the occupancy comfort. One such example is the implementation of Digital Twins technology for smart building management, combined with IoT by the Dubai Electricity & Water Authority (DEWA), to reduce water consumption by 50%.
Digital Twins in Industrial Facilities
According to the Supply Chain Management Outsource, there were over 10 million factories globally in 2019. While industry 4.0, Big Data, and IoT push many sectors to integrate advanced digital technology rapidly, Industrial Facilities are no exception. Leveraging Digital Twins can be used to advance both functional, operational, maintenance, and monitoring processes. The approach allows to simulate the behavior and performance of industrial facilities like power plants, manufacturing, warehousing as well as production facilities, allowing for production optimization, emissions and downtime reduction, risks management, and safety improvement. Today we already have some examples of potential large-scale implementations like the Siemens with NVIDIA partnership to create an industrial Metaverse that incorporates the Digital Twins technology combined with real-time data and IoT for innovative solutions to real-world issues.
Digital Twins in Shipping Industry
The cargo shipping market worldwide is estimated to reach $4.2 trillion by 2031. Maritime is among the most dynamic and challenging industries with an essential role and significant impact on the global economy, representing 80% of the volume of international trade. Considering the sector’s scale, Digital Twins can be vastly incorporated into many aspects, including supply chain, fleet control system, portal and terminal operations, safety and security, and tracking and monitoring operations. Digital Twins can be used to recreate the entire transporting freight process, with fully functional facilitates, vessels, scenarios of any scale commercial transportation, or even entire port operation. The technology enables to plan, predict, model, and asses routine and emergency operations, providing data-driven, safe test environments for specialists to collaborate remotely or on-location, allowing for reduced costs, increased planning and control process efficiency, taking preventive measures, and improved safety for both the personnel and the freight.
Digital Twins in Events, Tradeshows & Conferences
The global event industry has taken a significant toll due to the covid-caused restrictions, with many venues moving online. While this did shift the format from what we were used to, with more people adapting to the remote presence, the world moved back to being connected in person once the restrictions were lifted. Nevertheless, we have already tasted what it means to live with physical limits and online get-togethers. As technology advances, we are bound to see more hybrid, with combined online and offline presence, events, conferences, and tradeshows. The event market is projected to even out and surpass 2 trillion USD in 2028. Digital twins can be brought to events, tradeshows, and conferences of any scale as one of the technologies capable of helping to connect the digital and physical. Accessible through immersive experiences, Digital Twins can be used to illustrate large-scale projects, incentives, or advanced time-lapses, which could be especially helpful in energy conferences, manufacturing and construction trade shows, and architecture and design events. The approach can similarly be used to connect many online and offline attendees for entertainment events, including concerts and theatrical and circus performances.
Digital Twins in Transportation
The global transportation market continues its rapid growth, estimated to hit 15.94 trillion by 2032, and includes the transportation of people and goods. While the market is predicted to accelerate even further in development, we can see it, like other industries, benefiting greatly from incorporating the new technology. Digital twins can be used to create and test virtual models of road junctions, vehicles, traffic flow, transportation routes, and many more. Infused with real-time data, Digital Twins can help optimize performance, reduce fuel consumption, improve safety, and reduce risks, simulating people and vehicle behavior and different transportation scenarios. It allows for more effective and efficient resource planning, modeling, and testing of possible long-term issues in a virtual environment based on a real-life counterpart of the persons or goods.
Digital Twins in Logistics
Digital Twins are among the technology trends transforming the logistics industry, bringing new tools and capabilities. The global digital logistics market size is projected to land at 77.52 billion USD by 2030. The vast capabilities of this technology can be incorporated into any direction, starting from planning, modeling, and forecasting to complete supply chain support. Digital Twins can be used in logistics to help advance the planning and implement the detailed simulation into the operations and organization. The technology allows to model and incorporate transportation scenarios into the supply-chain management flow. Among other capabilities, the Digital Twins approach allows recreating and reenacting of options of goods transportation from the point of origin to the point of consumption, giving accurate data as output that can be used for assessment and decision making.
Digital Twins in Retail
Retail is one of the industries that is being heavily infused with digitalization. The global digital retail market is estimated to reach 902.88 billion by 2027. The vast incorporation includes e-commerce and traditional brick-and-mortar locations. As both markets are becoming increasingly competitive with more players entering, a wider variety of available goods, and matching price points, businesses seek to leverage technology to their advantage. Infusing retail with Digital Twins technology can help demonstrate products, advance merchandising, and enhance the shopping experience through digital overlays of traditional goods and services. It can add a close real-life physical layer to e-commerce goods, allowing consumers to hands-on experience items in the digital environment. The Digital Twins technology enables advanced storytelling, helping build a more engaging user experience, enhancing content, interactions, and visualization, and serving as a new means to connect with customers.
These are just a few examples of the many applications of digital twins in various industries. As technology continues to evolve, we are bound to face even more creative and innovative implementations in a wide range of industries across the globe. While these are the possible implementation directions, let’s look at some real case examples of Digital Twin technology implementation.
Medical VR Intubation Simulation
Medtronic McGRATH™ MAC VR Intubation Simulation is an interactive and immersive VR intubation simulation experience created with Medtronic to demonstrate the product and to train practitioners and medical students. It presents the usage of the McGRATH™ MAC video laryngoscope as a standard of care by educating participants on how to perform an intubation procedure with a variety of patients and the complexity of intubation scenarios. Find out more about the Medical VR Intubation Simulation here.
Aerospace VR Maintenance Simulation
The main objective of the project was to create a VR for jet turbine engine maintenance training environment for specialists in charge of regular technical reviews and checks of civil aircraft, including every step of the procedure from disassembling to cleaning, oiling, testing, and reassembling, in order to improve the quality of performed maintenance work. The simulation enables users to train and ensure process precision, reduce the number of corrective steps required, minimize engine post-maintenance release time, and process lead time. Find out more about the Aerospace VR Maintenance Simulation here.
Instrumentation Laboratory HemoCell in VR
The objective of the project was to create a VR environment constructor where the client could create 1-to-1 virtual visualizations of the future laboratory according to their customer’s requirements. The virtual space would allow customers to first-hand visit and observe the future laboratory with pre-installed equipment. Find out more about the Instrumentation Laboratory HemoCell in VR here.
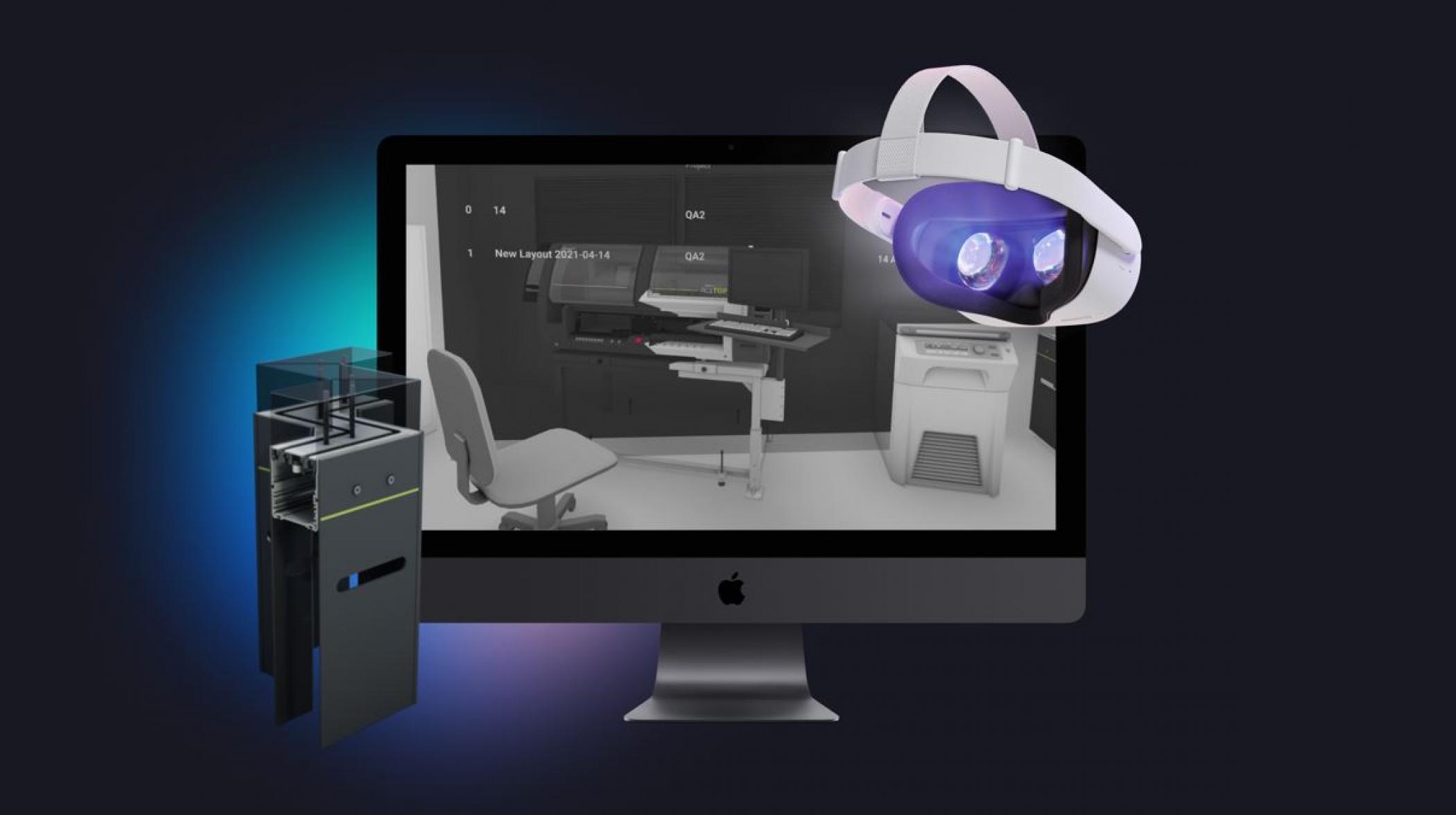
As the technology continues to evolve, more innovative use cases of projects that leverage digital twins will emerge, advancing processes, growing knowledge, and helping solve real-world problems.
Benefits of Digital Twins
As discussed, the Digital Twins approach can be implemented in various industries and at different scales, from creating Digital Twins for cities to matters that define chemical elements. The technology can deliver several benefits across industries, including:
-
Digital Twins Use to Improve Process Efficiency: Digital twins enable specialists to optimize performance and reduce downtime of physical systems and processes, resulting in increased efficiency and productivity.
-
Digital Twins Use to Refine Predictive Maintenance: With digital twins, on-site and remote specialists can monitor equipment in real-time and detect potential issues before they occur, enabling them to conduct maintenance proactively, reducing the risk of downtime, and saving related costs.
-
Digital Twins Use to Expedite Issue Resolution: In case of any issues or malfunctions, digital twins can provide specialists with insights into the root cause of the problem, reducing the time required to troubleshoot and resolve issues.
-
Digital Twins Use to Improve Design & Testing: Digital Twins allow to optimize design, modeling, and testing, especially if combined with a virtual environment. The pre-deployment run-through with the Digital Twin approach can help deliver comprehensive real-world solutions, reducing the need for physical prototypes and testing.
-
Digital Twins Use to Enhance Safety & Security: Digital twins can help model and identify potential risks, threats, and safety hazards, allowing to plan more effectively, mitigate risks and take preventative measures to improve safety and security.
-
Digital Twins Use to Increase Sustainability: By simulating different consumption and operation scenarios, digital twins can help plan and optimize energy usage, reduce waste, and improve sustainability.
Overall, digital twins can help organizations make more informed, risk-assessed decisions, while reducing costs, improve efficiency, safety, and sustainability. As a result, the adoption of Digital Twins technology is only expected to grow and accelerate amongst industries. This technological advancement will be especially curious to observe as a combination of the Digital Twins and the Metaverse.
FAQ
How Digital Twins Transforming More?
The Digital Twins approach can transform not just small fractions of the processes and training or education programs but entire industries. The technology can be used to recreate practically any real-life object, environment, or process, thus opening a significant window for optimization and advancement.
How Digital Twins Are Manufacturing Medicine?
The Digital Twins approach can be used in drug manufacturing to reenact various scenarios during development, testing, and production. They can help make processes more predictable, incorporating risk management scenarios and providing data-driven evaluations.
How Digital Twins Are?
Digital Twins are a digital replica of a physical environment, object, process, or asset. Depending on the actual need, they are built with different levels of detail and can incorporate full physical, operational, functional, and visual parameters.
How To Create Digital Twins?
Digital twins are created based on many input types, including 3D models, CAD or BIM models, 3D scans, or built from scratch. If the Digital Twins are part of an immersive environment, the developers must account for ergonomics, locomotion, interactivity, and other defining functions that will impact the level of immersion.
How Do Digital Twins Work?
Digital Twins work as 1-to-1 replicas of physical objects, assets, processes, and environments and serve as their digital counterparts. The technological approach is leveraged to optimize operations, design, test, reenact, adjust, plan, evaluate, and assess risks using real-world data input.
Conclusion
Digital Twins have emerged as a powerful technological tool amongst the rapidly growing industries responsible for quite a significant fraction of the global economy. Undoubtedly, the approach will continue proving itself more with every new project. We can only expect Digital Twin technology to grow in visual fidelity, complexity, and functionality. As digital twin technology evolves, we will witness even more innovative and impactful applications in amongst industries, driving innovation, digitalization, and the new era of Industry 4.0.
About Lucid Reality Labs
Lucid Reality Labs is a visionary XR development company that crafts complex immersive solutions through spatial technology – from concept & design to development & support, with a strategic focus on Healthcare, Life Science, Aerospace & Defense, and many more. We equip industries with the boundless potential of immersive technology. The Lucid Reality Labs’ Team believes that XR can contribute to the improvement of the quality of life for people around the globe. With our mission of disrupting global challenges with responsible technology, the company delivers solutions with impact that elevate industries with immersive capabilities. Check the award-winning use cases created by Lucid Reality Labs here.
Authors: Lucid Reality Labs marketing team & subject matter experts.